Choosing a Material for Your Flat Spring, Spring Clip, Contact or Other Metal Part
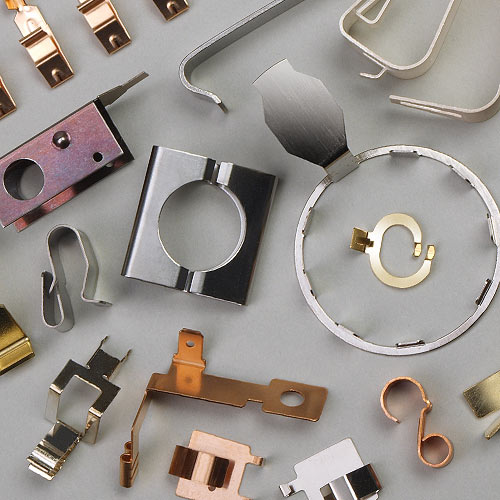
We are often asked to recommend a material for a customer’s flat spring, spring clip, battery contact, or other custom part. The standard response is that we do not make material recommendation, because the application requirements (e.g., spring force, conductivity, range of motion and corrosion resistance) are so critical to material selection. Our expertise lies in the manufacture of springs and stampings, not the design of the part for its intended function.
Rather, we suggest the materials that are viable alternatives relative to the manufacturability of a part. Many part geometries can be accomplished utilizing spring-tempered materials such as stainless steel, spring brass or phosphor bronze. When possible, these are preferable because they do not require heat treatment subsequent to forming, a process that can cause part distortion.
In other cases, the geometry of the part cannot be achieved with tempered material. Sometimes this is due to insufficient clearance to allow for the over-bending required to accommodate material spring back. In other instances, bend radii are too tight to achieve without material fracture. In these cases, material must be selected that can be formed in a softer state (annealed, for example) and heat treated to spring temper subsequent to forming. High-carbon steel, 410 stainless steel and beryllium copper are examples of heat-treatable (or precipitation-hardenable) materials.
Obviously, the application plays a major role in material determination. Flat springs for mechanical purposes are most commonly made from carbon steel or stainless steel. Those for electrical applications such as battery contacts are typically made from “red metals” for their superior electrical conductivity. Brass, phosphor bronze and beryllium copper are most often selected.
We at Fourslide are happy to discuss the alternatives with our customers and share the benefit of our many years of experience. Contact us any time to discuss your part requirements! Ultimately, however, the customer must consider all the characteristics and variables (tensile strength, yield strength, durability, cost) relative to the requirements of the application before making a material selection.